Minimum Distance Between Two Bends Sheet Metal
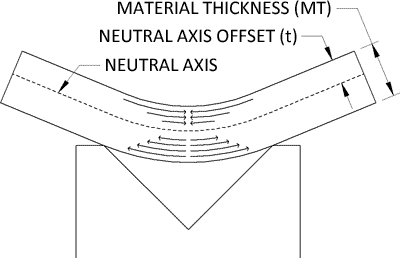
The minimum distance from a weld to a form is the spot diameter plus the bend radius.
Minimum distance between two bends sheet metal. The distance between the sheet metal bend line and edge of the hole should be two times or greater the thickness of the sheet metal. The more ductile the sheet metal the. Also spaces between pierced holes and bends should accommodate the bend radius h and be far enough from the bend. It is most economical to use a single bend radius throughout the design but if necessary you can utilize multiple radii.
The minimum distance between welds is 10 times the material thickness. Distance from outside mold line to the bottom of the cutout should be equal to the minimum flange length prescribed by the air bend force chart. A 7 67 b 0 5 minimum l bending 3 0. The minimum distance between a weld and the edge is two times the diameter of the spot weld.
Use this document to choose values that are both manufacturable and meet your needs. Bend radii minimum bend sizes. The sheet metal design rule of thumb in this case is. Minimum sheet metal bend radius depends on the selection of tool and the process.
The minimum distance between one dimple and another is four times the material thickness plus the inside radius of each dimple. Use pems instead of threaded inserts. The minimum distance between two counterbores is eight times the material thickness. Minimum sheet metal bending radius.
Whenever a increases by 1mm b increases 1 87 accordingly. The minimum distance that a dimple should be from a bend is two times the material thickness plus the inside radius of the dimple plus the radius of the bend. Center to center distance between two holes minimum center to center distance between two holes in sheet metal parts is required to avoid metal distortion deformation and fracturing. Recommended minimum distance between hole slot edge to bend in sheet metal design is three times the sheet thickness plus bend radius.
In low carbon steel sheet metal the minimum radius of a bend should be one half the material thickness or 0 80 mm 0 03 inch whichever is larger counterbores. The increasing relation between two sizes the longer a is the longer b is. Usually the preferred distance between holes and a bend is 1 5 times the sheet. Bending size shown in the following picture.
For open hem the bend will lose its roundness when the inside diameter is greater than the sheet metal thickness. 3 reduction formula empirical value of gooseneck punch 0 5mm sheet. Sheet metal design consideration dimple. For bends the minimum distance between the inside edge of the bend and the outside of the hem should be 5 times material thickness plus bend radius plus hem radius.